
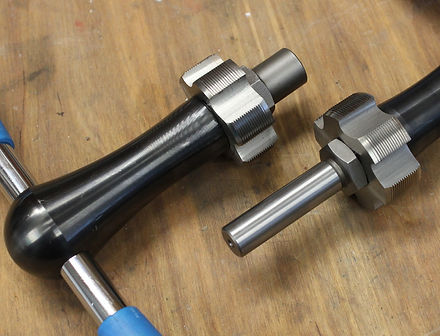

Frequently Asked Questions
1. Which materials do you build in?
As of now I am building only in steel. This is mainly because steel, among other frame materials, is the most suitable for custom fabrication, and have a ride which is sought after by a lot of passionate cyclists. And I think there is no question that it is the toughest and most durable one.
​
2. Did you have a training on framebuilding?
Yes. I’ve had courses on “Framebuilding” and “Fitting” at The Bicycle Academy; which is a leading institution on this subject.
​
3. Which construction methods do you use?
Currently I am building frames by only brazing; as I think this is the most elegant and creative method as well as it is functional. The brazing techniques I use are:
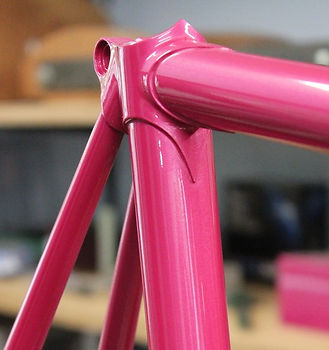
Lugged Joints:
The classical construction of steel frames.

Fillet Brazing:
The most frequently used technique in Brelis; pleasing appearance of lean and functional joints, tubes seemingly flowing into each other.

Bi-laminate:
The combination of two prior techniques; the fabricated semi-lugs fillet brazed into tubes, bring a fully customized look.
4. Which brand of supplies do you use on your frames?
For tubesets I use mostly Columbus and Reynolds, but also free to use other brands as well. For dropouts, braze-ons and such, I use parts of 4130 or stainless 630 (17/4) alloys from reputable suppliers like Paragon Machine Works, Long Shen etc
​
5. What is the ordering procedure and conditions?
There is detailed information in the Price List documents about this topic.
​
6. How does international orders work?
Ordering a custom frame internationally, the first thing to make sure is the “fit” to be perfect, as this is one of the main points of having a custom bike. If you already are sure of your fit with your current bike, I can design based on that without a problem. If you are not; still things are not hard either; I am always open to work with a local fitting specialist of your choice or with the fit data you are handed out by them.
​
The second part of course is the shipment of the finished frameset. I always hand it out with insurance and tracking to be on the safe side. I have experience shipping internationally too, so problems are unlikely. Even if in case, you will not be liable for any cost of damage or loss.
​
7. What are your warranty conditions?
Parts manufactured in the Brelis Workshop (like frame, fork, stem) have a lifetime warranty (of the product) against any manufacturing and design defects. Also I offer a crash replacement or repair discount.
​
But I have to add in a disclaimer; this warranty should not be interpreted as “your frame will be replaced in any case of failure by any means” as some big brands apply; who does most of their manufacturing in the far east and whose farme cost mostly is comprised of engineering, molding or overhead costs, and the actual material and labor cost of a frame may be negligible. So it is often not a big problem for those brands to replace a failed frame without so much investigation about the root cause of failure.
​
However for smaller custom workshops like Brelis, almost all of the cost of each frame is material and labor. So this warranty stated here is only and only valid in the cases where there is an open evidence of a manufacturing or design fault. So for a healthy evaluation, it is utmost important to stop using the problematic part immediately and transfer it to Brelis without any tampering.
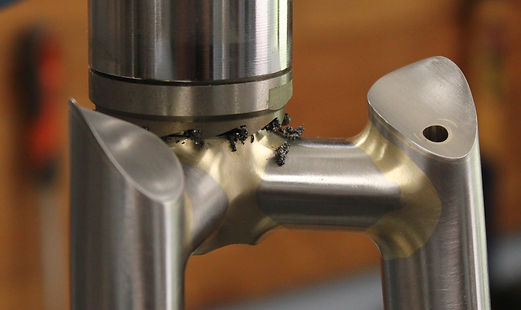